Es gibt einige Dinge, ohne die wäre eine Welt, wie wir sie heute kennen, völlig undenkbar. Nein, dazu gehören nicht nur moderne Entwicklungen wie Halbleiter, ohne die kein zeitgenössischer Computer möglich wäre. Es sind ebenso trivial anmutende Sachen wie das Gewinde, das Rad – und nicht zuletzt Metalle.
Ohne diese Element- und Werkstoffgruppe wäre unsere Zivilisation nicht bloß sprichwörtlich „nicht über die Steinzeit hinausgekommen“. Denn alles, was danach zwischen Kupfer-, Bronze- und Eisenzeit kam, wurde zutiefst von Metallischem bestimmt.
Tatsächlich sind Metalle, nicht nur aufgrund dieser historischen Bedeutung, die wichtigste Werkstoffgruppe in der Geschichte des Menschen. Grund genug, diese vergangene und künftige Bedeutung näher zu beleuchten.
Begriffskunde: Metalle, Legierungen und was sie ausmacht
Nicht jeder, der diese Zeilen liest, wird sich noch genau an den Sachkunde- oder Chemieunterricht erinnern. Zum Einstieg deshalb die wichtigsten Begriffe für besseres Verständnis.
- Erz: Eine in der Erdkruste vorhandene Kombination aus Mineralien (Gesteinen) und einem Metall bzw. einer metallbasierenden chemischen Verbindung (beispielsweise ein Oxid).
- Metalle: De facto nur die reinen Elemente, wie sie auf der Periodentafel definiert werden. Umgangssprachlich aber ebenso korrekt für alle:
- Metallwerkstoffe: Technisch nutzbare Materialien, die mehrheitlich auf Metall basieren. Bis auf wenige Ausnahmen handelt es sich dabei stets um Verbindungen mindestens zweier Metalle oder eines Metalls und anderer Elemente auf molekularer Ebene, eine sogenannte:
- Legierung: Durch gezieltes Aufschmelzen eines Metalls und Verbinden mit mindestens einem anderen Element entsteht eine Legierung, sofern dabei die primären Metalleigenschaften (siehe weiter unten) nicht verlorengehen. Ein Beispiel für eine typische Legierung, die umgangssprachlich häufig (und eigentlich falsch) Metall genannt wird, ist der:
- Stahl: Eine Legierung, die mehrheitlich aus Eisen und höchstens zwei Prozent Kohlenstoff basiert. Diese prozentuale Schwelle definiert, ob ein Stahl schmiedbar ist. Deutlich mehr als zwei Prozent Kohlenstoff lassen Gusseisen entstehen – leicht gießbar, aber nicht schmiedbar. Ebenso existieren Stähle mit deutlich komplexeren Legierungen als bloß Kohlenstoff.
- Edelstahl: Die Gesamtheit aller Stähle, bei denen die Elemente Phosphor und Schwefel jeweils nicht mehr als 0,025 Prozent Anteil haben. Jedoch nicht automatisch ein:
- Rostfreier Stahl: Stähle, die durch Legierungen mit wenig oxidierenden Metallen (etwa Chrom) deutlich langsamer rosten – allerdings dennoch rosten können, wenn der Zeitfaktor lang genug ist.
- Edelmetalle: Einige wenige Metalle (bzw. Elemente), die bei Raumtemperatur nicht mit Luft und Wasser reagieren.
- Gediegene Metalle: Elementar reine Metalle, die so in der Natur vorkommen. Hier sind keine chemischen Prozesse nötig, um das Metall von einem anderen Element abzuspalten. Eisen etwa kommt hauptsächlich in Form von Eisenoxid vor, daher ist es nötig, diesen Sauerstoffanteil abzutrennen.
- Primärmetalle: Metallwerkstoffe, die mehrheitlich aus gerade erst geförderten Anteilen bestehen.
- Sekundärmetalle: Metallwerkstoffe, die durch Recycling von Altmetallen gewonnen werden.
Wichtig: Wenn wir im Folgenden von „Metallen“ schreiben, dann sind damit ohne weitere Angaben Metallwerkstoffe bzw. Legierungen gemeint. Wo es um elementare Metalle geht, haben wir es kenntlich gemacht.
Doch was macht ein Metall oder einen Metallwerkstoff aus? Es ist das Vorhandensein von vier distinktiven Eigenschaften. Sie sind je nach Metall stärker oder schwächer ausgeprägt:
- Elektrische Leitfähigkeit: Absolut jedes Metall leitet elektrischen Strom.
- Thermische Leitfähigkeit: Metalle leiten Wärme und Kälte sehr gut, passen sich dadurch rasch ihrer Umgebungstemperatur an.
- Verformbarkeit: Metalle lassen sich in kaltem und/oder heißen Zustand leicht verformen, ohne dabei zu brechen.
- Spiegelglanz: Alle frisch gereinigten Metalle weisen einen signifikanten Glanz der Oberfläche auf, der sich je nach Intensität der Politur bis zur vollständigen Spiegelung steigern lässt.
Wo Legierungen hergestellt werden, geschieht dies häufig, um mindestens eine dieser Eigenschaften oder davon abgeleitete Eigenschaften zu verbessern. So wird beispielsweise Kupfer mit Zinn zu Bronze legiert, weil Kupfer allein zu leicht verformbar und nicht hart genug ist.
Metallbearbeitung: In Kürze zwischen Erzabbau und finalem Finish
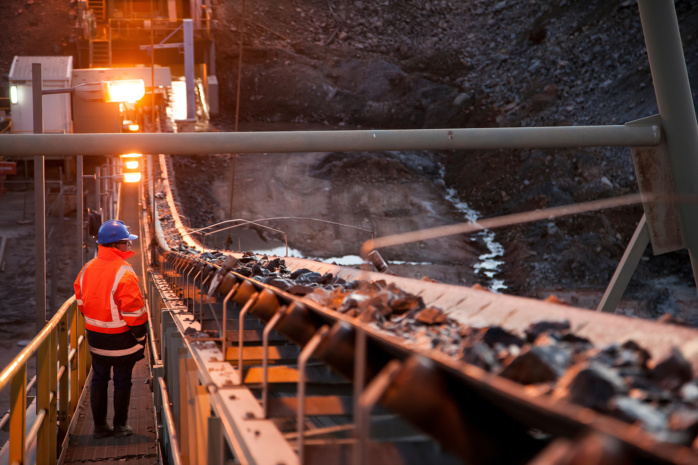
Ein wichtiger Grund, warum unsere urzeitlichen Vorfahren zu Beginn des Metallzeitalters einen solchen „Quantensprung“ erlebten, liegt darin, weil sie erst die Herstellungs- und Bearbeitungsverfahren erlernen mussten. Denn wie schon erwähnt kommen nur die wenigsten Metalle in gediegener, purer Form auf der Erde vor.
Naturgemäß muss man die gesamte Prozesskette mit etwas Vorsicht betrachten: Jedes Metall und vor allem jeder Metallwerkstoff benötigt und gestattet andere Schritte. Wo sich etwa Eisen nach dem Abbau relativ gut reinigen lässt, sind zur Herstellung von Aluminium einige komplexe chemische Verfahren notwendig – Hauptgrund, warum es erst seit dem 19. Jahrhundert genutzt werden kann.
Die folgende Auflistung der metallischen Prozesskette ist deshalb stark vereinfacht, lässt sich dafür jedoch auf recht viele Metallwerkstoffe gleichermaßen übertragen:
Abbau: Viele Metalle sind auf der Welt regional stark unterschiedlich verteilt. Sehr häufig sind sie in der Erdkruste in Gesteinen gebunden. Im ersten Schritt geht es darum, diese Gesteine zu finden und abzubauen. Hierzu kommt schwerste Technik zwischen Sprengstoffen und diversen Fördermaschinen zum Einsatz. Auch bei uns in Sachsen werden an verschiedenen Standorten unterschiedlichste Erze abgebaut.
Zerkleinerung und Homogenisierung: Über mehrere, teils gigantische Mahlwerke werden die Erzbrocken auf ein immer kleineres Maß gebracht. Dies vergrößert nicht zuletzt die Oberfläche der Körner, was die nächsten Arbeitsschritte vereinfacht. Vielfach wird bis zur Pulverform gemahlen. Durch sorgfältiges Vermengen mehrerer Chargen, Hinzugeben von Bindemitteln und gegebenenfalls Ofenbehandlungen entstehen Pellets mit definiertem Durchmesser und Rohmetallgehalt.
Gemischtrennung: Erzpulver bzw. Pellets werden in Hochöfen aufgeschmolzen. Dabei macht man sich die unterschiedlichen Dichten der Inhaltsstoffe zunutze. Ungewünschte Bestandteile schwimmen entweder auf oder sinken ab.
Reinigung: Mit je nach Metall unterschiedlichen Verfahren werden sämtliche anderen Verunreinigungen abgetrennt. Je nach Werkstoff kann dies ein mehrstufiger Prozess sein oder im selben Hochofen stattfinden. Bei der klassischen Roheisenherstellung wird beispielsweise Sauerstoff eingeblasen. Er reagiert mit überschüssigem Kohlenstoff zu Kohlendioxid.
Legieren: Durch die Zugabe von anderen reinen Metallen oder chemischen Elementen, aber ebenso sortenreinem Metallschrott, wird eine flüssige Legierung hergestellt. Damit ist die grundsätzliche Roh-Werkstoffherstellung abgeschlossen.
Urformen: Aus der unförmigen/flüssigen Rohmetallmasse wird, beispielsweise durch Gießen, ein fester, geometrisch definierter Körper hergestellt. Dies können Zwischenstufen sein, wie etwa Barren. Ebenso jedoch bereits hinsichtlich der Form nahe am Endprodukt liegende Halbzeuge.
Schmieden: Insbesondere (aber nicht ausschließlich) bei Stählen wird in warmem oder kaltem Zustand durch hohen, gezielten Druck eine Verformung erzielt. Sie dient einerseits dazu, die Endform des späteren Gegenstandes herzustellen. Andererseits verändert sich durch den Druck das Metallgefüge, was seine Materialeigenschaften optimieren kann. Neben dem Schmieden können weitere, aber ebenfalls immer ohne Materialverlust auskommende Verfahren angewendet werden – zusammengefasst unter dem Dachbegriff „Umformen“.
Wärmebehandlung: Durch gezieltes Erhitzen und Abkühlen/Abschrecken können die Eigenschaften einer Legierung weiter eingestellt werden – etwa in Richtung größere Härte oder Zähigkeit.
Spanabhebende Bearbeitung: Dieser Schritt kann je nach Metall und Endprodukt durchaus vor der Wärmebehandlung stehen. Immer geht es darum, durch unterschiedliche spanabhebende Verfahren überschüssiges Material abzutragen. Teils geschieht dies, etwa durch Drehen und Fräsen, zur Herstellung endgültiger Formen. Teils aber ebenso, um das Produkt nutzbar zu machen – beispielsweise durch das Schärfen einer Klinge. Ebenso kann hierdurch ein weiteres Ziel erreicht werden:
Oberflächenbearbeitung/-veredelung: Mithilfe von spanabhebenden Verfahren wie dem Polieren oder durch das Beschichten mit diversen Stoffen zwischen anderen Metallen (etwa Verzinken) oder Materialien (beispielsweise Lackieren) wird die Oberfläche des Produkts ausgestaltet. Dies kann sowohl optischen als auch praktischen Gründen dienen. Etwa, wenn ein nicht rostträger Stahl dadurch besser vor Oxidation geschützt wird.
Mitunter kann es zwischen den Schritten 8 und 10 noch nötig sein, einen zusätzlichen Fügeschritt zu integrieren. Hierzu werden mehrere Metallhalbzeuge auf irgendeine Weise miteinander verbunden, um das fertige Produkt herzustellen. Hierunter fällt beispielsweise das Verschweißen oder das Schneiden von Gewinden, damit ein Bauteil festgeschraubt werden kann.
Wie bereits angesprochen: In der Praxis kann jeder dieser Schritte je nach Metall und Endprodukt stark unterschiedliche Ausprägungen und Herangehensweisen aufweisen. Das ist allerdings ebenso einer der Gründe, warum Metalle heute so allgegenwärtig sind.
Sie lassen sich auf zahllose Arten bearbeiten, kombinieren und nutzen. Fast kein anderes technisches Material weist eine so große Vielfalt auf, die gleichermaßen mit den ursprünglichen metallischen Eigenschaften zusammenfällt.
So können beispielsweise Kunststoffe zwar ebenso durch Wärmezugabe erweicht und sehr leicht verformt werden. Ihnen mangelt es jedoch völlig an der elektrischen Leitfähigkeit und der großen Härte bei gleichzeitiger Zähigkeit und Temperaturstabilität.
Eine lange Geschichte: Der Mensch und das Metall
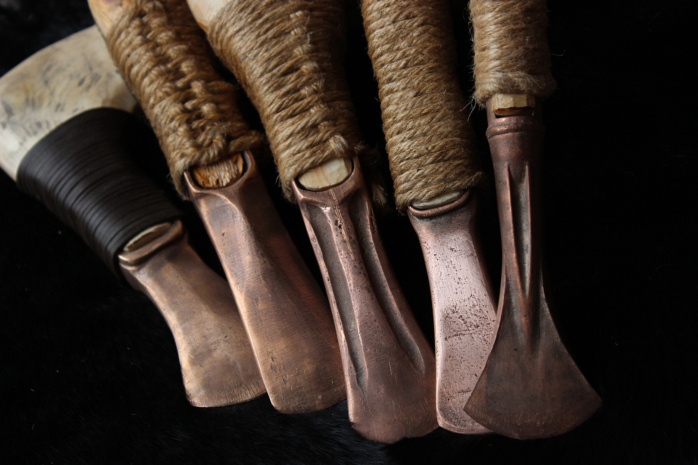
Wer das vorangegangene Kapitel aufmerksam gelesen hat, dürfte verstehen, warum zwischen dem ersten Auftreten des Homo Sapiens und dem frühesten Beginn einer Metallherstellung gut und gerne 290.000 Jahre vergingen – die ältesten Homo-Sapiens-Funde datieren auf 300.000 Jahre vor unserer Gegenwart; das Metallzeitalter begann zirka 7.500 Jahre vor Christi Geburt und somit dem Beginn unserer Zeitrechnung.
Nicht nur mussten unsere Vorfahren überhaupt erst einmal gediegene und erzgebundene Metalle erkennen können. Sie mussten zudem komplexe Techniken und Prozesse entwickeln, um letztere aus dem Gestein zu extrahieren – häufig noch in unterschiedlichen Weltregionen, wodurch viele Entdeckungen mehrfach getätigt wurden.
Insofern ist das menschliche Metallzeitalter, das definitionsgemäß bis zum Mittelalter reicht, auf die gesamte Geschichte des modernen Menschen bezogen nur äußerst kurz. Dafür allerdings geschah in diesen nur wenigen tausend Jahren buchstäblich Weltveränderndes.
Hinweis: Die genannten Zeiträume spiegeln den derzeitigen Stand der Archäologie; sie sind also nicht zwingend abschließend.
Die Frühzeit – als Metalle vom Himmel fielen
Schon bevor der Mensch eine grundlegende Ahnung von der Metallherstellung hatte, nutzte er sie bereits vereinzelt:
- Insbesondere Gold, Silber und Kupfer treten auf der Erde in gediegener Form auf. Alle drei Metalle sind zudem sehr weich und dadurch selbst mit prähistorischen (Stein-)Werkzeugen gut zu bearbeiten.
- Einfache Eisenlegierungen mit Nickel finden sich immer wieder durch Einschlag entsprechender Meteoriten.
Naturgemäß waren diese Funde äußerst spärlich – trotzdem und weil die steinzeitliche Erdbevölkerung schätzungsweise gerade einmal fünf Millionen Menschen umfasste. Dementsprechend waren solche Metalle dort, wo man sie nutzte, unglaublich kostbar – andererseits mangels Verfügbarkeit kaum für den täglichen Gebrauch relevant.
Von den urzeitlichen Kulturen des damaligen Nahen Ostens etwa ist eine mehrheitlich kultische oder dekorative Nutzung bekannt. Nur selten und räumlich stark begrenzt wurden praktisch nutzbare Werkzeuge und Waffen daraus gefertigt.
Von der Kupfer- und Stein- bis zur Eisenzeit im Überblick
Schon zu Beginn der Jungsteinzeit, also grob 10.000 bis 6.500 Jahre vor Beginn der Zeitrechnung, wurde vereinzelt gediegenes Kupfer zur Werkzeug- und Waffenherstellung genutzt. Diese Epoche war dennoch für alle späteren wichtig. Denn in der Jungsteinzeit erlernte der Mensch das Brennen von Ton zu Keramik – und dadurch gezielten Umgang mit und die Wirkung von Hitze zur Herstellung eines verbesserten Materials.
Ungefähr um 7.500 v. Chr. herum geschah im Gebiet des heutigen Anatoliens und Mesopotamiens jedoch der Schritt vom stein- zum metallverarbeitenden modernen Menschen. Dort war man bereits in der Keramikherstellung sehr erfahren. In der Folge entwickelten die dort lebenden Menschen die Fertigkeit, Kupfer nicht nur in regelrechten Minen abzubauen, sondern es in simplen Hochöfen zu verhütten. Ab zirka 5.000 v. Chr. waren importierte Kupferprodukte bis in unsere Breiten vorgedrungen. Darauf deuten Funde im heutigen Österreich und Tschechien hin.
Bis jedoch hier ebenfalls Kupfer abgebaut und Produkte daraus gefertigt wurden, dauerte es noch einige Jahrhunderte:
- Ab zirka 4.000 v. Chr. wurde in der Region importiertes Rohkupfer verarbeitet.
- Ab zirka 3.800 v. Chr. begannen die ersten Kupferbergbaubestrebungen.
Diese sogenannte Kupfersteinzeit war deshalb revolutionär, weil sie es den jeweiligen Kulturen ermöglichte, bislang ungekannte leistungsfähige und haltbare Ackergeräte zu fertigen. Der Pflug existierte zwar damals schon in Kulturen, die noch kein Kupfer nutzten.
Doch erst, als er mit dem Metall beschlagen werden konnte, war es möglich, damit harte Erde umzubrechen. Dementsprechend konnten solche Kulturen aufgrund des verbesserten Nahrungsangebots stark prosperieren – ein Grund, warum das damalige Ägypten und Mesopotamien bereits Hochkulturen hervorbringen konnten.
Doch ist Kupfer, wie angesprochen, recht weich. Indem verschiedene Völker immer feinere Metallurgie beherrschten, konnten sie nicht nur bessere Legierungen herstellen: Erstmals in der Menschheitsgeschichte bildeten sich spezialisierte Berufe heraus, entstanden weit gespannte Handelsnetze und Monopole in Regionen, die besseren Zugang zu Rohstoffen und mehr Wissen hatten.
Dies definierte die nächste Epoche der Menschheitsgeschichte: Ab zirka 2.700 v. Chr. gelang es in Ägypten erstmals, Kupfer mit Zinn zu verhütten. Es entstand Bronze, die ungleich härter ist und dadurch noch überlegenere Werkzeuge und Waffen gestattete – das Bronzezeitalter begann.
Um 1.200 v. Chr. wiederum begann in derselben Region das Eisenzeitalter. Eisen und daraus bestehende Legierungen benötigen deutlich höhere Temperaturen, sind also viel schwieriger zu beherrschen. Entsprechend war die Überlegenheit eisenherstellender Kulturen noch größer als die Differenz zwischen Bronze und Kupfer.
Zeitstrahl: Das Metallzeitalter | |||||
(Überschneidungen durch regional/kulturell unterschiedliche Start- und Endpunkte) | |||||
Name | Kupfersteinzeit | Frühe Bronzezeit | Mittlere Bronzezeit | Späte Bronzezeit | Eisenzeit |
Zeitraum (v. Chr.) | 5.500 – 2.200 | 2.200 – 1.600 | 1.600 – 1.300 | 1.300 – 800 | 1.200 – 1025 n. Chr. |
Die Industrialisierung: Metall wird Massenware
In dieser Form wurden verschiedene Metalle bis ins 18. und 19. Jahrhundert sehr traditionell hergestellt. Das bedeutet, in einer stark auf Handarbeit setzenden, manufakturartigen Fertigung. Mit Beginn der Industrialisierung standen jedoch nicht nur neue Möglichkeiten offen, sondern entstand ein gigantischer Bedarf.
Verdeutlichen lässt sich das anhand zweier Zahlen:
- Um 1700 produzierte Großbritannien etwa 12.000 Tonnen Eisen jährlich.
- Um 1850 belief sich die britische Fertigung auf über zwei Millionen Tonnen.
Ähnlich sah es bei vielen anderen Metallen aus. Eisen und Stahl waren jedoch nicht weniger als das Fundament der Industrialisierung und somit der modernen industriellen Welt und Lebensweise – ähnlich wie Kupfer aufgrund seiner besonders hohen Leitfähigkeit das Fundament der globalen Elektrifizierung wurde.
Metalle und die Zukunft – kein „altes Eisen“
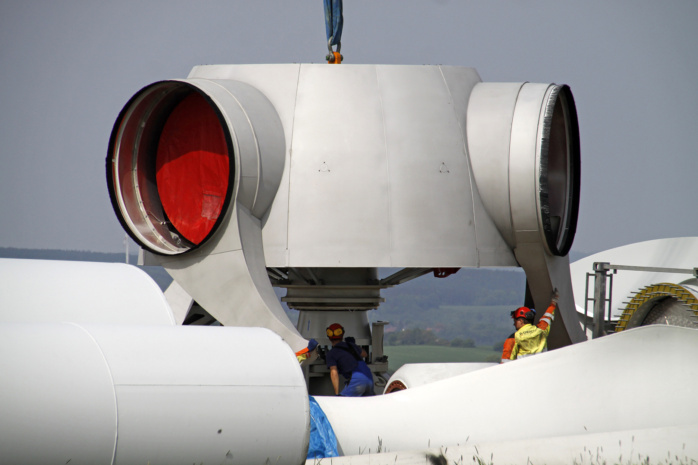
Der geneigte Leser muss sich nur umschauen, um wahrscheinlich Dutzende Metallprodukte in seiner Umgebung zu finden. Zwar haben sich die globalen Zentren der Schwerindustrie und somit der Metallfertigung seit dem Ende des Zweiten Weltkriegs (1939 bis 1945) deutlich verlagert.
Die seit der Industrialisierung so bedeutsamen westlichen Nationen waren dabei die Leidtragenden. Stahl etwa wird in überwiegendem Maß in Asien produziert – nicht mehr so sehr Europa und Nordamerika. Bei vielen anderen Metallen zeigt sich ein vergleichbares Bild.
Völlig falsch wäre es jedoch, dadurch auf ein baldiges Ende der metallischen Epoche des Menschen zu schließen.
- Wahr ist, dass man seit einigen Jahrzehnten immer mehr alternative Materialien erfindet und nutzt. Etwa, weil sie bei gleichen mechanischen Eigenschaften leichter sind.
- Wahr ist ebenfalls der große ökologische Fußabdruck zwischen Abbau und Endbearbeitung von Metallprodukten. Dies betrifft landschaftliche Verheerungen ebenso wie Treibhausgasemissionen.
Dennoch lässt sich selbst von schärfsten „Metallgegnern“ kein Ende absehen. Dazu muss zunächst auf einen Faktor hingewiesen werden: Kaum ein anderer Stoff lässt sich so leicht und umfassend recyceln wie Metalle. Egal wie komplex eine Legierung aufgebaut sein mag, sie lässt sich immer wieder und wieder einschmelzen, in ihre einzelnen Metalle auftrennen und zu einer neuen Legierung zusammensetzen – fast ohne Materialverluste.
Die Grenze wird nur durch die Wirtschaftlichkeit definiert. Also beispielsweise das, was das Abtrennen eines recycelten Metalls im Vergleich zur Herstellung eines Primärmetalls kosten würde. Aus diesem Grund befinden sich beispielsweise beim Aluminium geschätzt drei Viertel aller jemals gefertigten Massen nach wie vor irgendwo im Metallkreislauf.
Zudem werden gerade beträchtliche Anstrengungen unternommen, um neue Verfahren zu etablieren, die gerade das Thema Treibhausgasemissionen vermindern. So wird beim Stahl derzeit intensiv die sogenannte Wasserstoffroute im Testbetrieb evaluiert.
Sachsen ist dabei einer von Deutschlands Vorreitern. Die Nutzung von Wasserstoff zur Reduktion des Sauerstoffs verhindert das sonst auftretende enorme Freisetzen von Kohlendioxid – CO2. Wird grüner Wasserstoff genutzt, ließe sich somit tatsächlich klimaneutraler Stahl herstellen. Eine große Hoffnung, nicht zuletzt, um nicht noch mehr Marktanteile nach Asien zu verlieren.
Allerdings gibt es noch mehr Gründe, warum der Mensch noch in fernster Zukunft auf Metalle setzen wird: Es gibt schlicht keine andere Werkstoffgruppe, die all diese positiven Eigenschaften liefert, dabei jedoch keine untragbaren Nachteile mit sich bringt. Allein, was die Zukunft der Elektrik anbelangt, sind Kupfer und Co. schlichtweg nicht substituierbar, weil sie Leitfähigkeit mit niedrigsten Preisen verbinden.
Die wichtigste Materialgruppe des modernen Menschen ist daher „gekommen, um zu bleiben“. Sie wird den Homo Sapiens deshalb mutmaßlich so lange begleiten, wie er als eigenständige Art besteht.
Von den ersten Grabstöcken, die mit einer Spitze aus gediegenem Kupfer versehen waren, bis in die Gegenwart war es ein sehr weiter Schritt. Ein Schritt jedoch, ohne den die Entwicklung der Spezies Mensch einen völlig anderen Weg genommen hätte – definitiv nicht zu ihrem Besseren. Metalle sind heute trotz aller Konkurrenz nach wie vor die wichtigsten Werkstoffe überhaupt.
Und selbst, wenn sie aufgrund ihrer energieintensiven Herstellung von einigen Seiten scharf in der Kritik stehen, so sind sie auf vollkommen unabsehbare Zeit hinaus buchstäblich „alternativlos“ – und das in zahllosen Millionen Anwendungen.
Keine Kommentare bisher